Molybdenum disulfide (MoS2) is commonly used as a dry lubricant due to its enhanced performance in the absence of oxygen and its elevated temperature stability, which make it suitable for extreme environmental conditions. For these reasons, MoS2 has well-established applications in the automotive and aerospace industries, metal forming and cutting tools, electrical contacts, and nano- and micro-electromechanical systems.*
In this context, it is well-known that crystalline forms of MoS2 have better frictional properties as compared to amorphous ones. They are also less sensitive to humidity and atmospheric conditions.*
However, crystalline MoS2 tends to exfoliate during sliding if the loading forces are too high, resulting in high wear, coefficient of friction (COF), and low stability. To improve the design and durability of components based on MoS2 there is a need to explore the tribological behavior of MoS2 in alternative forms, and to characterize their early-stage wear behavior down to the nanoscale.*
Experimental characterizations such as those made possible by atomic force microscopy (AFM) are the most important tool to gain quantitative insights on the wear resistance of those materials on the nanoscale.*
In the article “A comparative nanotribological investigation on amorphous and polycrystalline forms of MoS2” by Hesam Khaksar, Prashant Mittal, Nabil Daghbouj, Grzegorz Cios, Tomas Polcar and Enrico Gnecco, the wear behavior of two amorphous and polycrystalline forms of MoS2 prepared by magnetron sputtering is characterized in a combined nanoindentation and atomic force microscopy (AFM) study supported by Raman and transmission electron microscopy (TEM) analysis.*
From the morphology of wear tracks estimated after scratching the surfaces with a Berkovich indenter and a loading force up to 2 mN, the authors conclude that, on the microscale, both forms follow the Archard’s wear equation, and the wear resistance is about four times higher on the amorphous MoS2.*
The coefficient of friction is much lower on the worn areas, which is associated to significant smoothing of the surfaces caused by the scratching process. With normal forces in the µN range, the analysis is made difficult by the fact that the linear dimensions of the wear tracks are comparable to those of the smallest surface features.
Even if the Archard’s equation looses validity, the wear resistance is considerably larger on amorphous MoS2 also on the nanoscale.*
The results presented by Hesam Khaksar et al. conclude that the polycrystalline form of MoS2 has poor tribological properties at the micro/-nanoscale as compared to the amorphous form and hence less suited as a solid coating in ambient conditions.*
NANOSENSORS™ diamond coated PointProbe®Plus DT-NCHR AFM probes (typical force constant: 80 n/m, typical macroscopic AFM tip radius of curvature between 100 and 200 nm) were used to create the scratches and capture the images, allowing for a detailed examination of the surface features and material properties.
For AFM-based friction measurements, NANOSENSORS™ PointProbe®Plus PPP-LFMR AFM probes, with a typical force constant of 0.2 N/m were employed.
NANOSENSORS™ PointProbe®Plus PPP-NCHR AFM probes (typical force constant: 42 N/m typical resonance frequency 330 kHz) were used for standard tapping mode imaging.
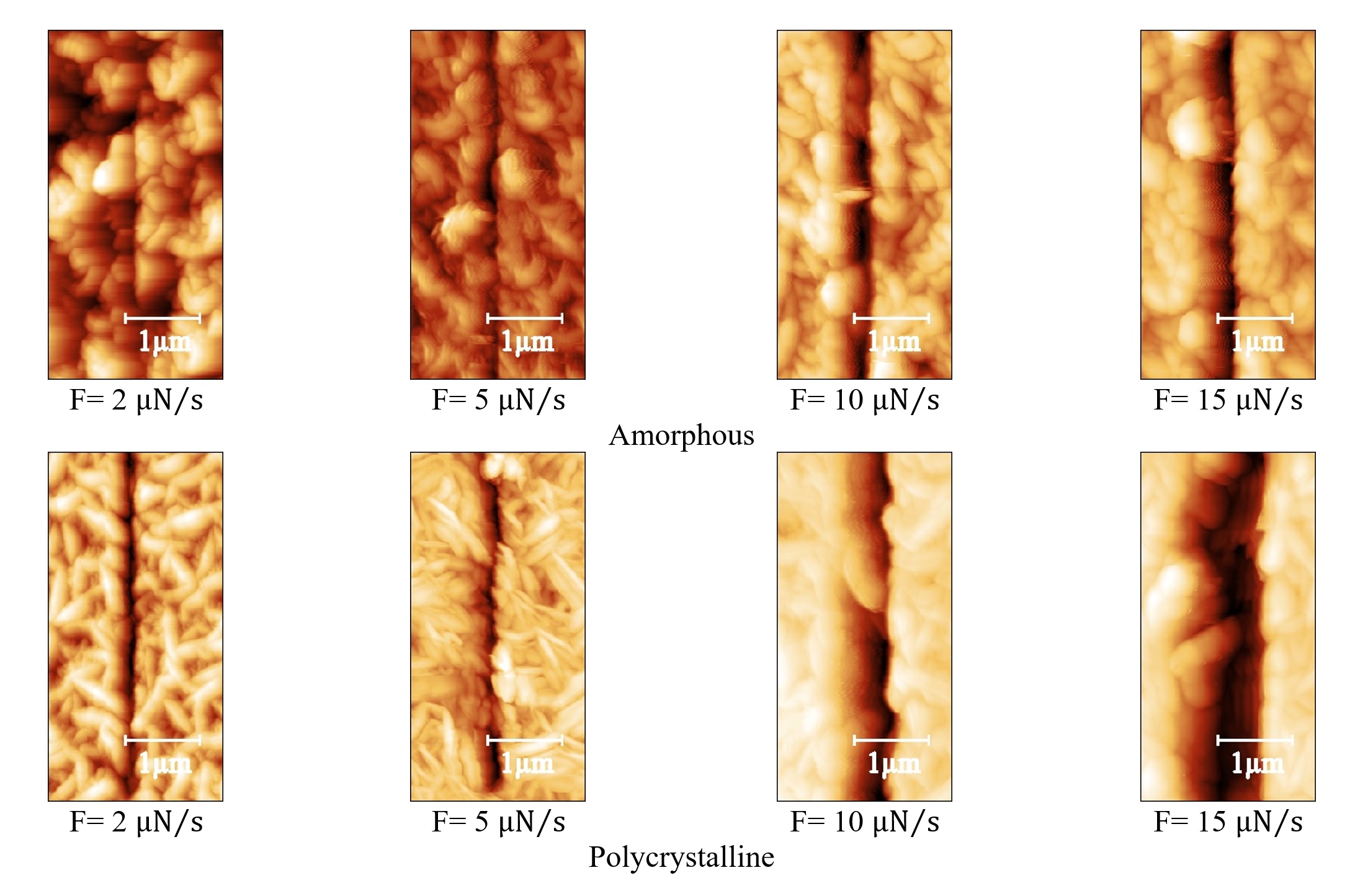
Figure S5 from Hesam Khaksar et al. 2024 “A comparative nanotribological investigation on amorphous and polycrystalline forms of MoS2”:
AFM image on the scratched area with the AFM (contact mode image)
Fig. S5 shows a collection of images captured by the atomic force microscope, which displays scratches on two different materials. The first row shows scratches on amorphous material, while the second row shows scratches on polycrystalline material. Within each row, the force used to create the scratches was increased from 2 to 15 μN . The NANOSENSORS DT-NCHR AFM cantilever was used to create the scratches and capture the images, allowing for a detailed examination of the surface features and material properties.
*Hesam Khaksar, Prashant Mittal, Nabil Daghbouj, Grzegorz Cios, Tomas Polcar and Enrico Gnecco
A comparative nanotribological investigation on amorphous and polycrystalline forms of MoS2
Applied Surface Science, Volume 672, 1 November 2024, 160842
DOI: https://doi.org/10.1016/j.apsusc.2024.160842
The article “A comparative nanotribological investigation on amorphous and polycrystalline forms of MoS2” by Hesam Khaksar, Prashant Mittal, Nabil Daghbouj, Grzegorz Cios, Tomas Polcar and Enrico Gnecco is licensed under a Creative Commons Attribution 4.0 International License, which permits use, sharing, adaptation, distribution and reproduction in any medium or format, as long as you give appropriate credit to the original author(s) and the source, provide a link to the Creative Commons license, and indicate if changes were made. The images or other third-party material in this article are included in the article’s Creative Commons license, unless indicated otherwise in a credit line to the material. If material is not included in the article’s Creative Commons license and your intended use is not permitted by statutory regulation or exceeds the permitted use, you will need to obtain permission directly from the copyright holder. To view a copy of this license, visit https://creativecommons.org/licenses/by/4.0/.